As mentioned in a previous article (linkedin post: https://www.linkedin.com/posts/eric-balligand-0bab042_est-ce-la-fin-de-la-qualit%C3%A9-quelques-r%C3%A9flexions-activity-7167876081209884673-ovgx?utm_source=share&utm_medium=member_desktop) about the setbacks of a major American aircraft manufacturer, quality management must once again become a priority for companies and evolve rapidly by adapting to digital transformation and increasing demands on safety, environment and customer experience.
Between digitalization, the integration of cutting-edge technologies and a global approach to performance, companies must quickly redefine their quality strategies to remain competitive and responsible.
1. Towards a Proactive and Predictive Approach: The Shift from Control to Anticipation
Traditionally, quality control focused on detecting defects after they appeared in the production phase. Today, the evolution towards a predictive approach based on risk analysis (“risk-based”) radically transforms this paradigm:
- 1.1: Risk analysis or “Risk-Based Thinking”: Taken up by the ISO 9001:2015 standard, this concept invites the identification, evaluation and mitigation of risks from the product design phase. It is not a new concept but it was still underused and is now experiencing a resurgence of interest as its effectiveness is formidable for those who use it at the right time and with the right level of expertise.
- 1.2: Design for Quality: As its name suggests, design quality assurance starts from the design phase and allows with various milestones throughout the product development process to secure and verify the quality and the response to the customer’s requirements before the manufacturing of the first prototypes, thus preparing the industrialization phase in the best possible way.
- 1.3: Strengthening the role of the project/product quality manager: this goes hand in hand with the 2 previous points, the missions and responsibilities of the project/product quality manager are strengthened and extended, he is the keeper of the final quality of the product and the response to the customer’s requirements.
- 1.4: “Right First Time” and “Zero Defect” strategies: These approaches aim to design robust processes to limit rework and avoid non-conformities from the first manufacturing and will take up the first two points and add other tools to limit variability.
This transition to upstream, anticipatory quality results will drive a reduction in costs related to errors, better risk management and ultimately an improvement in customer satisfaction.
2.Quality 4.0: When Digital Reinvents Quality
As we are talking about Industry 4.0, we could mention the concept of Quality 4.0 embodying this transition to digitalized quality management.
- 2.1: Big Data and Artificial Intelligence (AI): The explosion of data recorded, measured, and their volumes, now makes it possible to anticipate defects before they turn into major problems through predictive analysis. The use of “big data” processing is expected to multiply in the coming years, but it will still be necessary to use it correctly! Today, 80% of the data collected is not used!
- 2.2: Internet of Things (IoT) and Automation: Smart sensors and collaborative robots are increasingly used on production lines to perform automated quality controls, reducing human error and optimizing processes.
- 2.3: Traceability and Blockchain: The management of configurations, product changes, traceability, environmental impact, security needs become critical elements that must be imperatively under control with the use of adapted processes and tools, they can be further strengthened by the use of blockchain.
This integration of technologies not only makes it possible to react more quickly to malfunctions, but above all to establish a proactive approach, placing prevention at the heart of industrial strategies.
3. Agility and Collaboration: A New Culture of Quality Management
With more and more software and electronics in our products, agility, long associated with IT development, is now fully invited into the field of quality:
- 3.1: Agile methods applied to quality: These methods allow teams to quickly adapt to changes and continuously optimize processes through real-time feedback and short design loops. The quality role in this approach is critical and is becoming increasingly strong.
- 3.2: Digitalized Kaizen culture: Continuous improvement is reinforced by collaborative digital tools, facilitating the identification and implementation of immediate corrective actions. “Digitalized and collaborative” project management application offers are multiplying on the internet and are now accessible from smartphones!
- 3.3: Participation of operational teams: The involvement of all stakeholders – from operators to managers – is becoming essential to establish a real dynamic of continuous improvement. This cannot be ordered and must be the subject of a strategy adapted to the context and challenges of the company with a real “involving” communication policy.
Quality management is thus transformed into a collective and evolving process, where each employee plays a key role in achieving common objectives.
4.Quality at the Heart of Sustainability and Responsibility Issues
Today, companies are no longer satisfied with aiming for economic performance; They must also meet the increasing number of environmental and societal requirements through:
- 4.1: Integration of environmental standards: Certifications such as ISO 14001 and ISO 50001 demonstrate the desire to integrate environmental performance into quality management.
- 4.2: ESG (Environmental, Social and Governance) indicators : These indicators make it possible to measure and value the contribution of quality approaches to corporate social responsibility objectives.
- 4.3: Sustainable Quality and the Circular Economy: More and more industries are integrating processes that ensure that recycled or refurbished products meet strict quality standards.
This new alignment between quality and sustainable development meets the growing demand of consumers and stakeholders, while ensuring long-term competitiveness, but requires the development of new processes and the building of an associated quality approach!
5.Conclusion
The transformation of quality management is a perfect example of the shift towards a smarter, more agile and responsible industry. By combining cutting-edge technologies, proactive methods and a collaborative culture, companies are redefining quality as a strategic lever essential to their success.
In a context where the pressure to reduce costs, produce more and faster, these new approaches demonstrate that investing in quality is not only a regulatory obligation, but a winning choice essential to ensure the sustainability and reputation of the company.
And you, where are you with this approach?
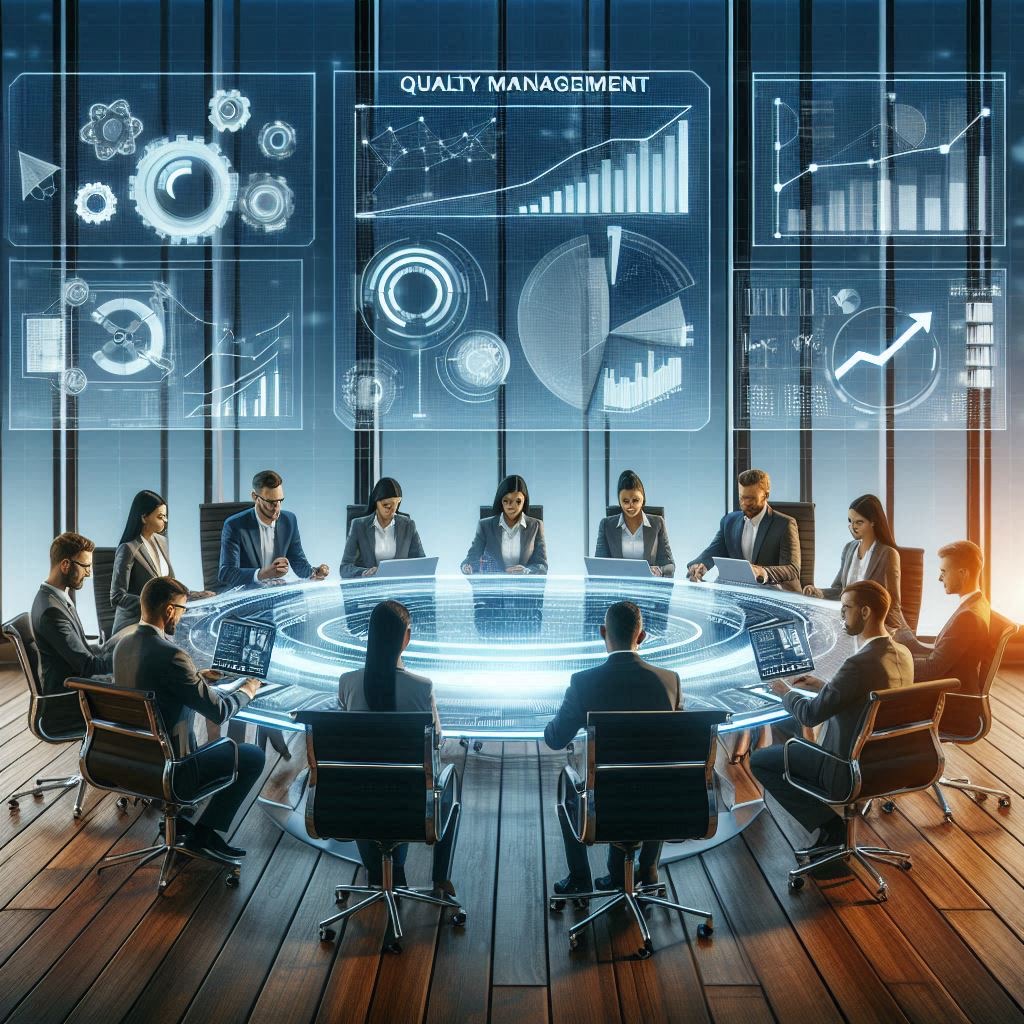
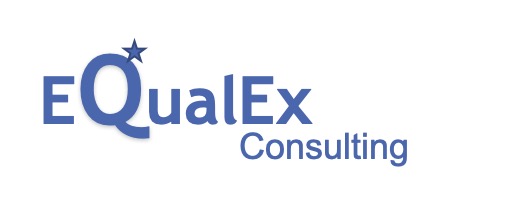